The production process of tungsten carbide blade typically involves the following steps: 1. Powder preparation: Tungsten carbide is made by mixing tungsten powder and carbon powder in a furnace, where they are heated to high temperatures to form a hard and dense material. 2. Mixing: The tungsten carbide powder is mixed with a binder material such as cobalt, nickel, or iron. The binder acts as a glue to hold the tungsten carbide particles together. 3. Pressing: The mixture of tungsten carbide and binder is compressed into a mold using high pressure. This creates a solid block of tungsten carbide that is later cut into the shape of the blade. 4. Sintering: The compressed tungsten carbide and binder mixture is heated to high temperatures in a sintering furnace. This process melts the binder material and causes it to fuse with the tungsten carbide particles, creating a solid and durable blade. 5. Grinding and finishing: After sintering, the tungsten carbide blade is ground to the desired shape and size using precision machinery. The blade is then polished and finished to ensure that it has a smooth surface and precise cutting edges. Overall, the production of tungsten carbide blades requires careful attention to each step of the process to create a blade that is both strong and precise.
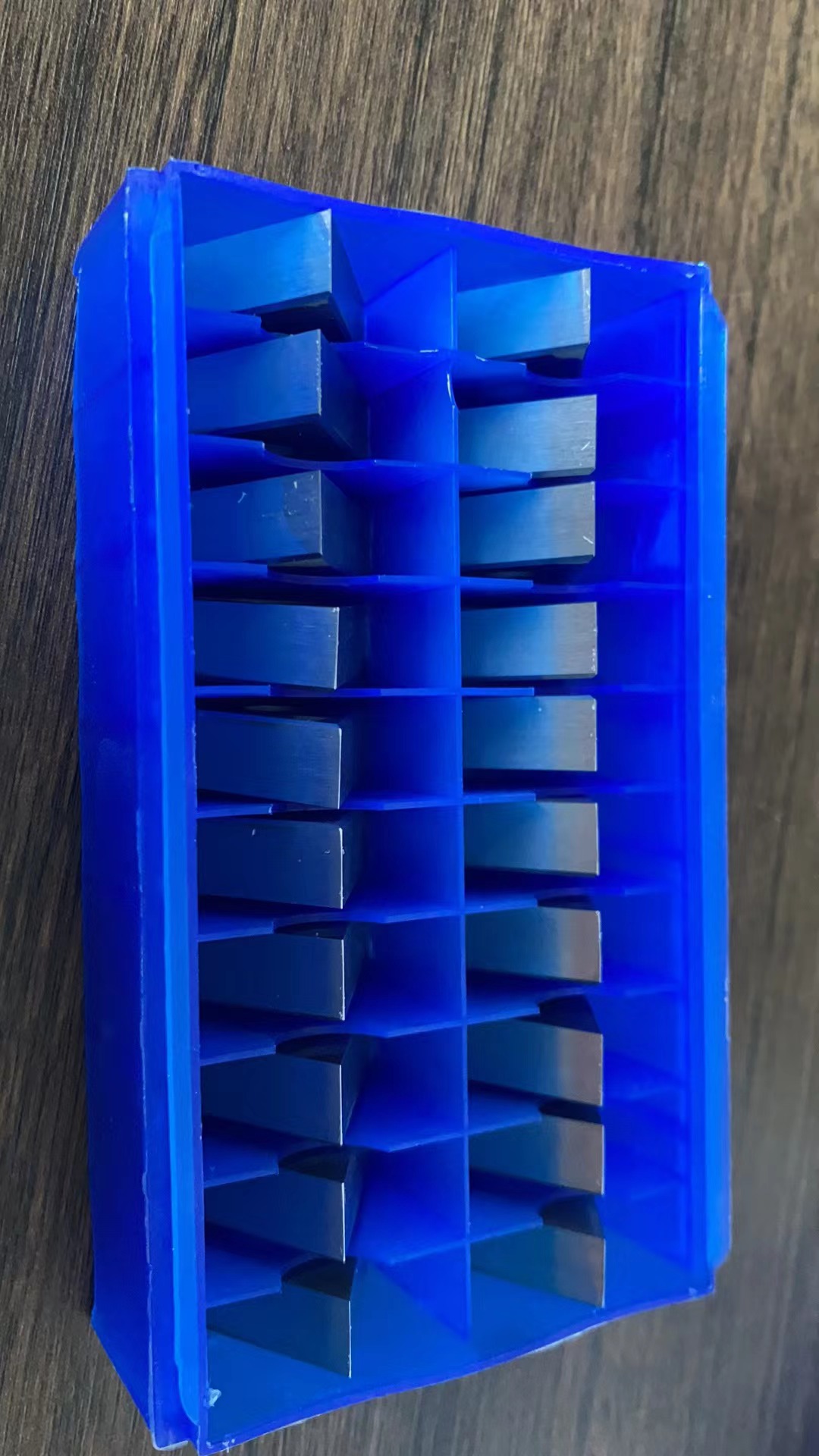
Post time: Apr-21-2023